December: it’s inventory time. Planning the organization of the warehouse is a key issue and it should not be underestimated. Automating to optimizing management? Let’s plan it.
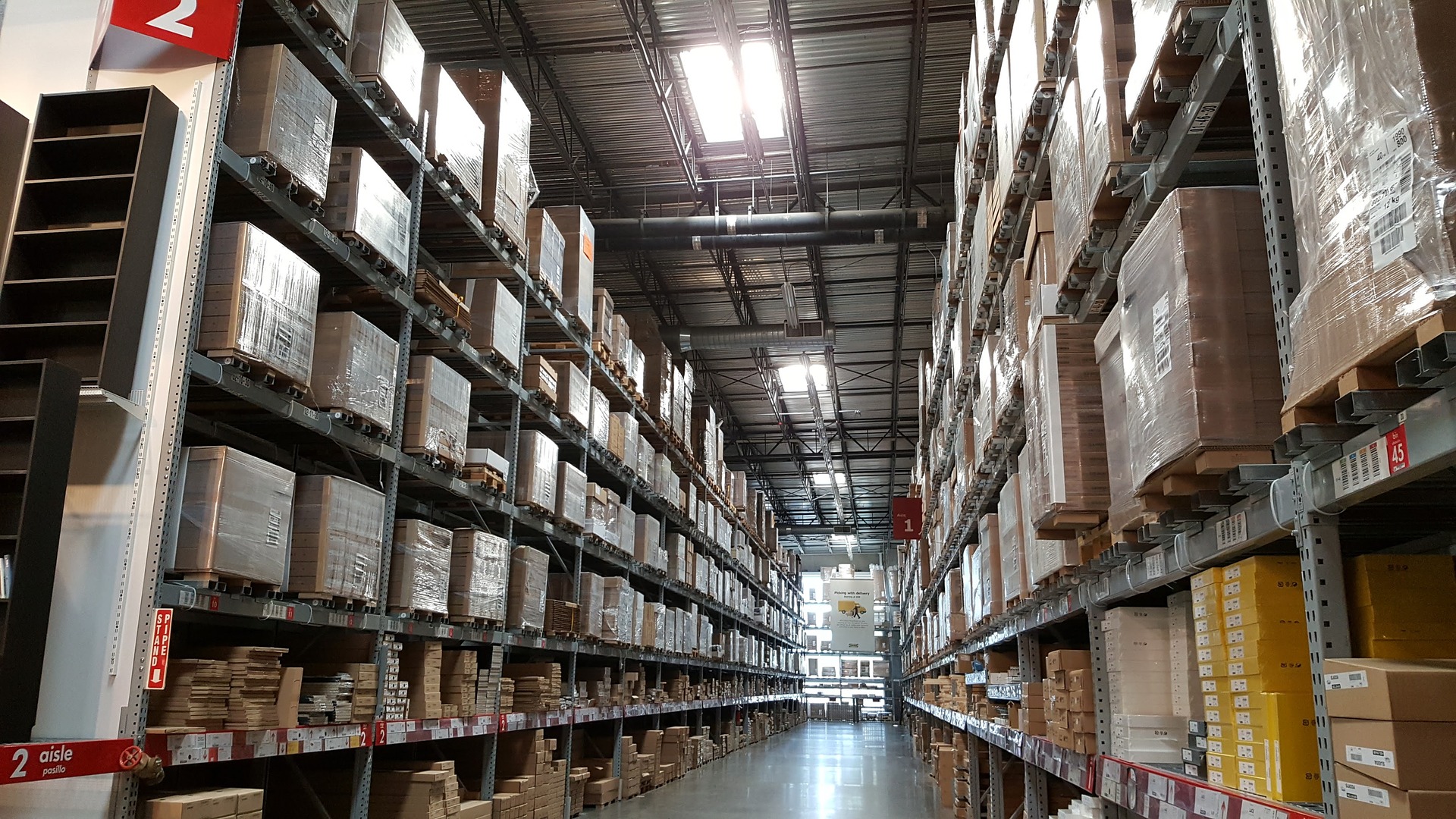
December: it’s inventory time. Warehouse organization, for high standards of technology.
There are rumors saying that a systematic and rational organization of the warehouse is not that important. Somewhat superficially, it is believed that warehouse management has nothing to do with the improvement of technology standards and sophistication.
However, we are far from reality…
With this simplistic attitude, one glosses over all the important consequences that could result within the company. The organization of the warehouse is, in fact, a pivotal aspect for every company, large and small, as well as its management.
In this article, we will try to clarify some aspects concerning inventory.
December, it’s inventory time: how to organize your warehouse inventory
December has arrived: the month of Christmas, holidays to spend with family and loved ones, and since it closes the year, warehouse inventory.
Let’s analyze the aspects of one of the fundamental activities that every business must deal with at the end of the year. Important to efficiently prepare the company for the years to come.
The practice of inventory or stocktaking, to use a more international term, involves first of all the analysis of inventories. Inventories are the goods intended for sale, or used to create products for resale, that remain in stock at the close of the financial year.
They can be classified as follows:
- Raw materials and semi-finished goods
- Consumable materials and supplies
- Products in process
- Goods for resale
- Finished goods
December, it’s inventory time. Far from simple
When the time comes to draw up the final financial statements of a company’s financial year, it is also necessary to record the physical quantities of goods in inventory that must be valued.
This is also regulated by Article 2426, No. 9 of the Civil Code, which requires inventories to be valued in the financial statements at the lower of purchase or production cost and market-deductible realizable value.
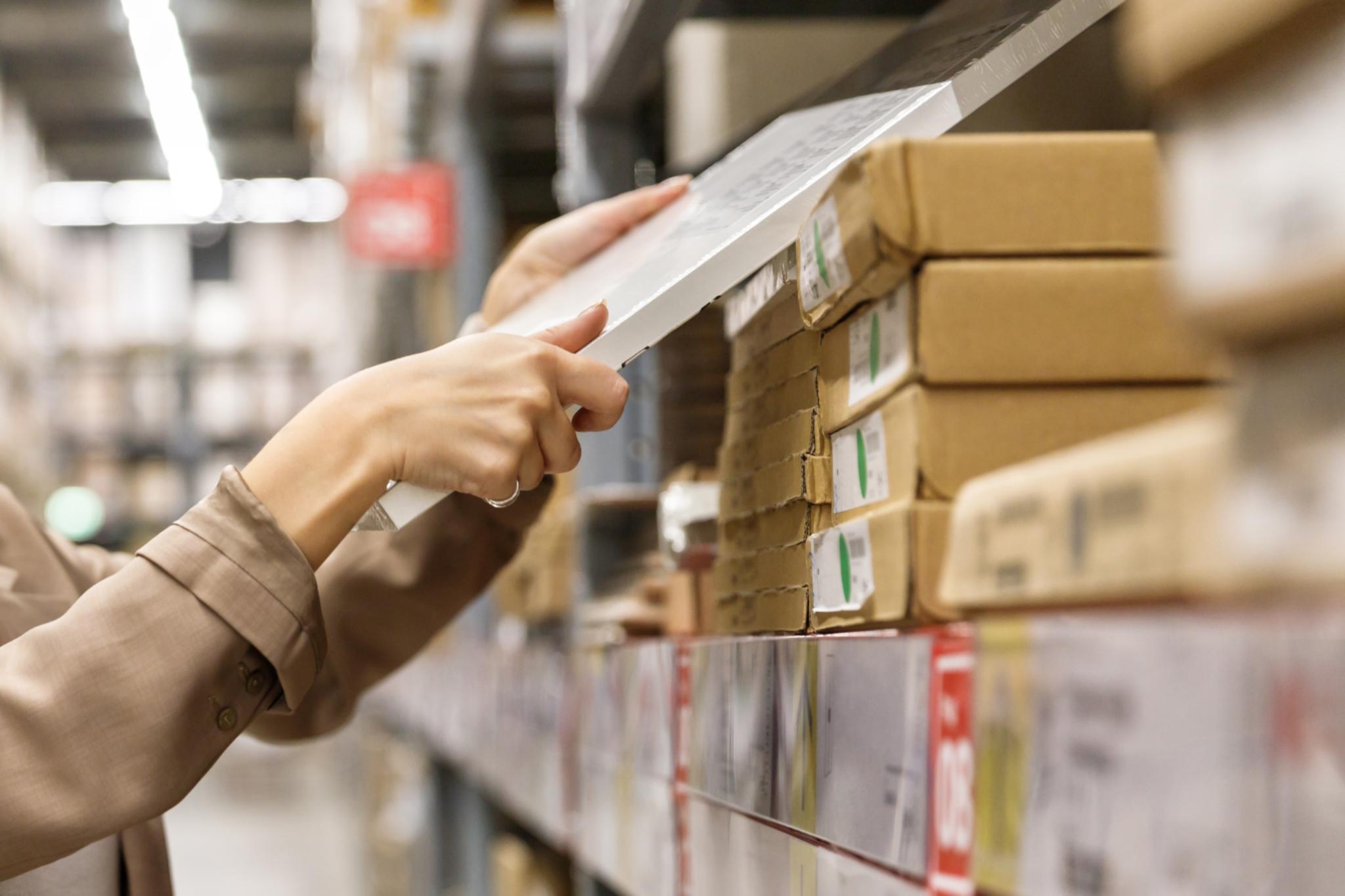
Whether it is a small/medium-sized business or more complex and articulated entities, doing the inventory is a process that can be complicated.
It is usually a hated activity for those who must organize it, and it is often considered superfluous compared to other activities that are apparently more profitable for the company’s own business.
December, it’s inventory time: a must-have practice
In contrast to what it might seem, it is impossible to give up stock inventory: having stock under control at the end of a given period allows you to avoid problems with production and reorders. This is especially true for those who run an online e-commerce, as for them inventory is essential to reduce the differences between physical and accounting inventories.
Let’s also not forget that keeping inventory records is mandatory in some cases.
Pursuant to Article 14 co. 1(d) of Presidential Decree 600/1973 and Article 1 of Presidential Decree 695/1996, in fact, the following are obliged to keep auxiliary inventory records:
– corporations;
– public and private commercial entities;
– non-commercial entities, limited to commercial activity;
– partnerships and persons treated as such in ordinary accounting;
– individuals engaged in business activities in ordinary accounting;
– nonresident entities, limited to commercial activities carried out in Italy through permanent establishments;
These categories, in order to be held to the obligation, must exceed certain values of revenues and inventories. At this point the regulations become more specific to clarify the different positions. It is better to say that they specify certain business requirements. Overall, as always, the regulations become complex when not obscure and incomprehensible. The tendency that arises is look at this type of practice as something unmanageable.
There is good news, however! Since 2019, it has been possible to manage a warehouse in a faster, simpler and more accurate way, thanks to technologies and digitization, which have undoubtedly favored the process of automating practices.
Let us now analyze the benefits of rational and orderly warehouse management.
December, it’s inventory time: the benefits
Ensuring the efficiency of the production process
An effective inventory must be accurate and periodic. If it is carried out consistently, following scheduled deadlines, it will allow optimizing the control of goods processed and received, ensuring a fast and functional service that will be appreciated by customers.
Knowing inventories
Whether inventory management is imprecise and not constant, it will create discrepancies and doubts about inventories, with all the problems that come with it.
A key aspect of monitoring the situation in the warehouse is order: an accurate tracking of operations, as well as a periodic general audit.
Modalities and tools for warehouse inventory
There are several ways to prepare a warehouse inventory. There is no single modality and each company, depending on the size and structure of the warehouse, must find the best one for its size and type.
Let’s look at the most used ones:
Pen and paper: the traditional tools
You can start with paper, pen and calculator.
Nowadays outclassed by the most digital environments, they should continue to be the basis. They are traditional tools, but irreplaceable as the basis for keeping stock under control, especially for smaller realities.
Whether the tools are pen and paper or the more sophisticated systems, it always starts with categorizing products. The second step is to further subdivide the products that sell out most quickly. This will help to keep an eye on the categories that need more frequent reorders. It’s also useful to note next to each macro category the names of the suppliers and the minimum stock level required.
Now it’s time to label the shelves and catalog products in special charts that can clearly show the physical breakdown within the warehouse.
How? For instance, by indicating for each product the following information:
- category to which it belongs,
- date of arrival,
- cost,
- quantity,
Of course, it is essential to update the tables periodically to avoid errors.
Digital tools: Excel
In the absence of management software, a very performant tool is the Excel Sheet, which allows you to manage the warehouse quickly and easily.
Among other things, this tool will make it possible to have detailed summary charts that will optimize control at the end of the year.
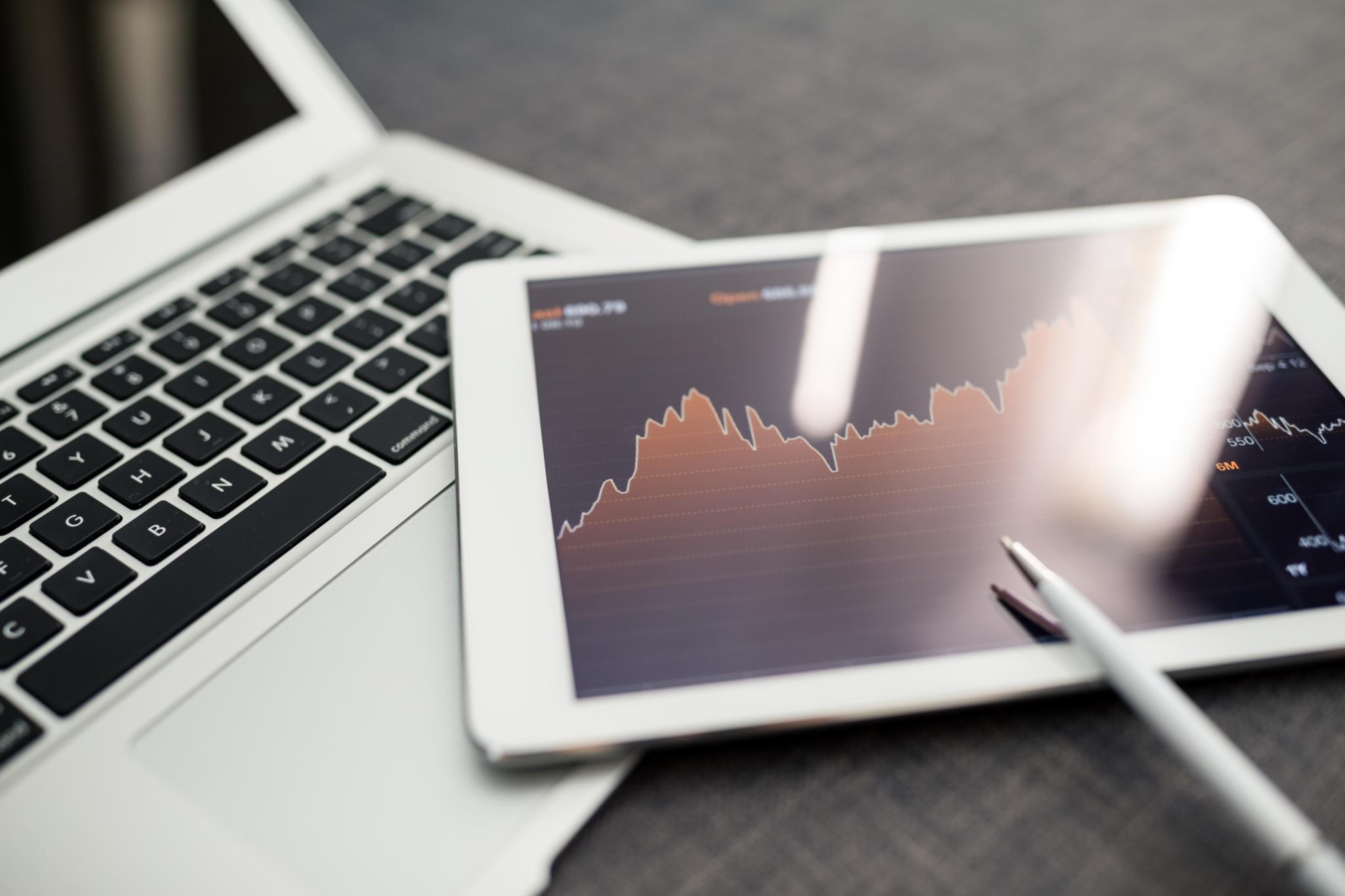
To create the warehouse inventory with Excel, three different sheets must be used:
– one for products, where to list them with their respective information
-one for loading operations, with the date of arrival and quantity in the warehouse
– one for the selling of the goods
If a warehouse deals with both semi-finished and finished products, it is advisable to use three sheets for each category. The sheets should then be linked together for an overall view in order to help eliminate the risk of errors and delays.
It is also possible to automate these operations.
There are multiple online Excel sheet templates, pre-filled and very practical. Needless to say, it is essential that the sheets are constantly updated.
The most complete choice: management software
Not only the optimal, practical and fastest, but also the most accurate choice, which is inevitable in a larger and more structured warehouse: the management software.
With such a tool, it is possible to control every internal warehouse operation, greatly simplifying and speeding up inventory activity, thanks to process automation.
Controlling inventory with constantly updated management software will also optimize and speed up calculation operations at the end of the fiscal year.
In addition, management software allows historical storage. This will make it possible to trace back and detect any errors quickly and easily.
This tool can be customized according to business needs and different production flows.
Automation, for a competitive company
As already pointed out several times, if we want to increase the competitiveness of our company in the market, we must start precisely from an optimized organization of the warehouse.
Among warehouse management criteria, the one dedicated to automation is to be considered among the most effective performance principles.
However, like any serious and structured process, it needs careful planning. In order to proceed in a strategic and structured way, a detailed analysis of business needs is necessary, starting right from the warehouse.
The second step, which is no less important, is the evaluation of the budget: choosing an automated system even for inventory requires sometimes significant investments, and the so-called ROI could be recovered in a rather long time.
Choosing the right, reliable and punctual partner can be a choice that can allow the company to keep costs down and have precise control of inventory through B2B platforms such as the one offered by our portal, especially at the beginning of the business.
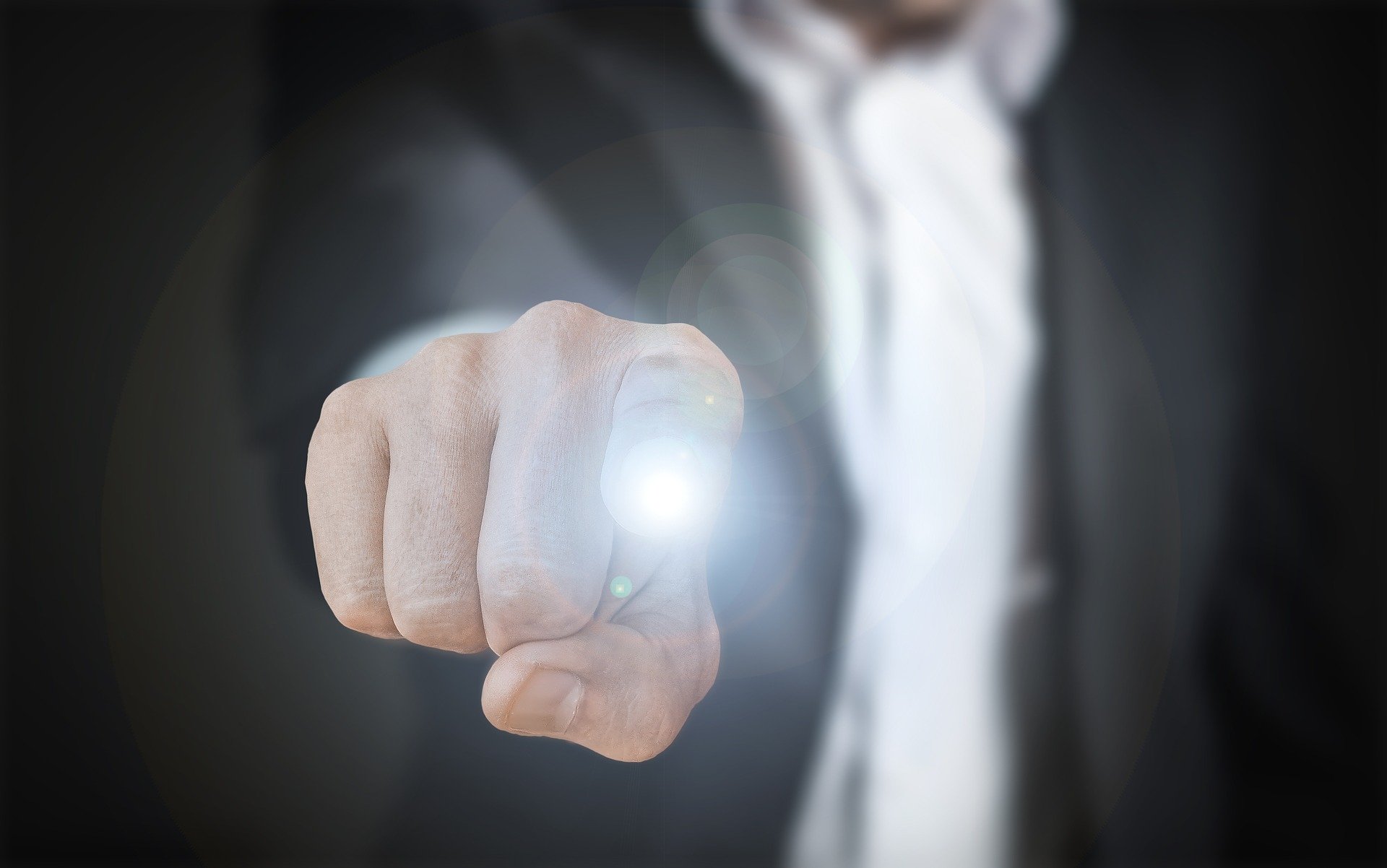
That’s why, choosing a supplier who knows how to manage its products and inventory is crucial for your business!
With that said, for the coming year, choose Tamarri S.r.l.
🎅 Tamarri S.r.l. wishes you a peaceful Christmas, full of the brightest plans for the year to come! 🎄